Pushing the boundaries of high-power Li-ion battery technology in the energy transition
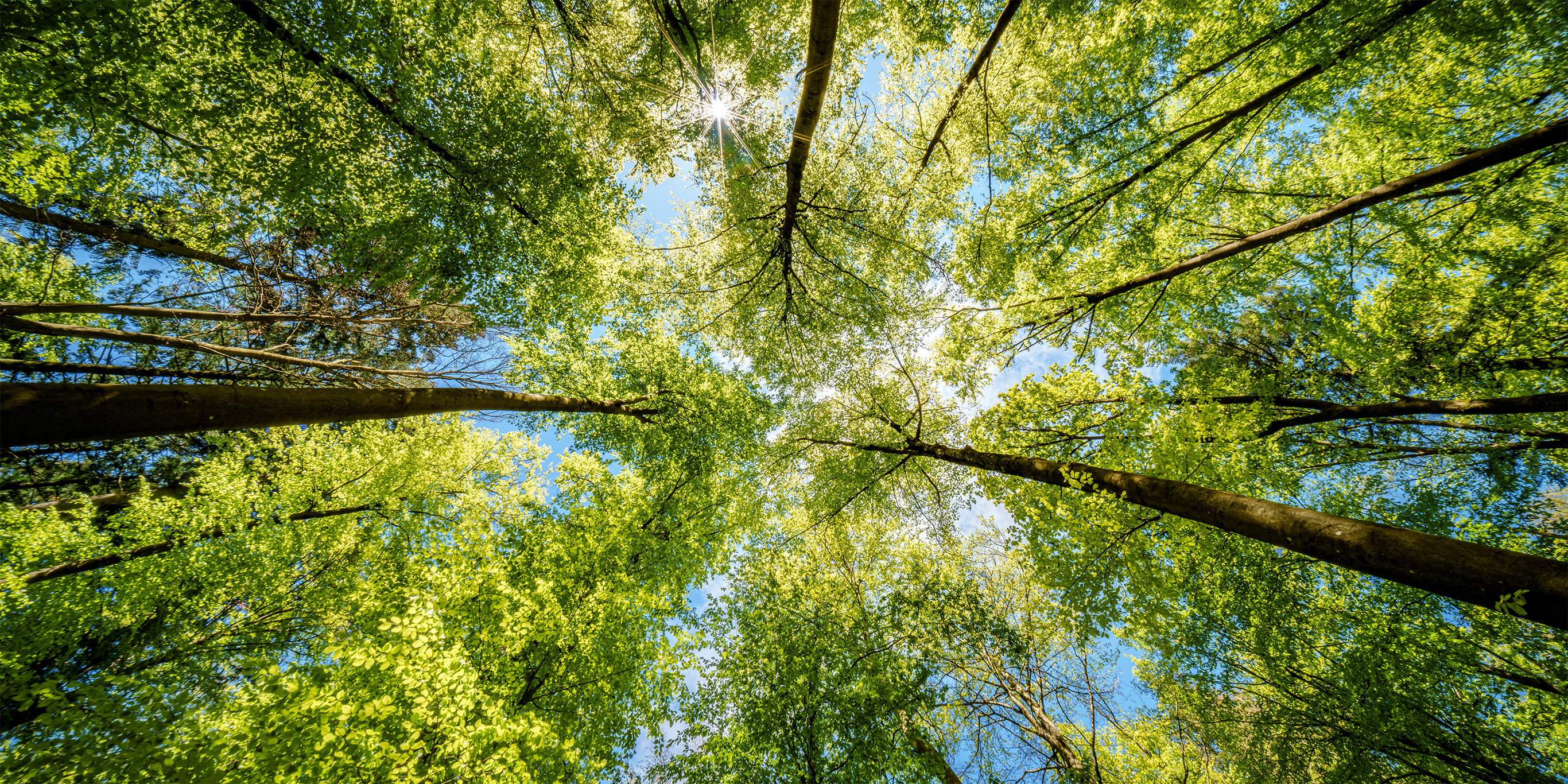
The low carbon energy transition is essential for the planet’s survival. To achieve the targeted warming limit of 1.5 degrees Celsius, the world must reduce carbon dioxide (CO₂) emissions, increase renewables in the energy mix from 28% today to 90% and, accelerate the adoption of electric vehicles (EVs) to practically replace all fossil fuel cars by 2050 [1]. Lithium-ion (Li-ion) batteries are a crucial technology in this global agenda as they provide an efficient and scalable solution for decarbonising transportation (passenger and heavy duty) and storing energy for renewables and AI data centres.
However, the widespread adoption of Li-ion batteries has significant challenges related to the unprecedented demand for critical minerals. In this blog we will touch on some of the environmental and social impacts associated with the extraction, refining and processing of these resources. We will also explain how Nyobolt’s innovative approach in the design of its proprietary anode materials, the engineering of its holistic battery systems, and the planning of its circular life cycle deliver an industry-first ultra high-power battery system that solves decarbonisation goals in challenging industries with an aim to have a net positive impact on the environment.
The challenges in sourcing critical raw materials
The Li-ion battery demand is projected to increase ninefold by 2040. This requires an unprecedented supply of critical raw materials, particularly lithium, cobalt, nickel, and graphite. Individually, the demand for lithium would grow globally 42-fold by 2040, graphite 25-fold, cobalt 21-fold and nickel 19-fold [2].
The mining and refining of critical raw materials generate a series of environmental and social tensions. Most of the available sources are geographically concentrated in a few countries with geopolitical implications (i.e. bottlenecks in the supply chains, increasing competition and trade tensions) and high import dependence for regions like Europe or the US [3]. For example, 94% of lithium production comes from Australia, Chile and China and the refining capacity is mostly concentrated in China. The Democratic Republic of Congo (DRC) accounts for more than 60% of the cobalt production. Manganese production is dominated by South Africa, Australia and Gabon and nickel is mined from Indonesia, Philippines, and Russia whilst the refining capacity is also concentrated in China, followed by Finland, and Indonesia. The graphite mining production and processing (natural and synthetic) in China accounts for approximately 75% of global graphite supply [4]. In 2023, China has imposed an export restriction on certain graphite products affecting the global supply chain for anodes.
From an environmental point of view, mining and refining activities generate high greenhouse gas (GHG) emissions as they are energy intensive and mostly run on fossil fuels. In fact, it is estimated that around 60 to 65% of the carbon footprint in Li-ion batteries comes from mining raw materials [5]. Hand in hand with the carbon footprint, mining activities have impacts that without adequate mitigation and prevention policies, can negatively affect the health and well-being of local communities, the biodiversity, and availability of clean water sources. In some locations, mining activities are linked to human rights violations, exploitative labor practices, corruption, and financing of armed conflicts [6]. As Li-ion batteries are massively adopted in different technologies, extending the usable life cycle, recycling critical raw materials, and searching for alternative new materials are important priorities that must be considered by the stakeholders in the supply chain.
Innovation and research that improves the lifecycle sustainability of Li-ion batteries
Nyobolt is a pioneer in the research and development of novel material science used in Li-ion batteries. Since 2019, the company has developed proprietary ultra-fast charging, long cycle life battery technology based on innovations in metal oxide and graphite-dominant anode materials. While both anode innovations deliver extremely high-power density that enables full charge cycles under five minutes without compromising safety or lifetime, Nyobolt’s proprietary niobium-tungsten-based metal oxide material has the fastest lithium-ion diffusion ever measured, delivering charge rates (C) up to 20C, or roughly twenty times the power of incumbent Li-ion battery chemistries
- Breakthrough material science not only provides high-power charging solutions where barriers to electrification suffer from reduced operational efficiency from charging downtime but also contribute to expanding familiarity and access to new uses for novel raw materials within the supply chain. Niobium for instance, is a critical raw material that has gained relevance over the past years from its uses in MRI magnets to Li-ion batteries. Most of the production originates from Brazil and its versatility provides several possibilities for green technologies and for designing recycling routes that would allow the diversification of the supply and the reduction of carbon footprint from mining. Tungsten is a refractory metal with the highest melting point among all elements and high density, thermal conductivity and mechanical properties at elevated temperatures. Tungsten resources are relatively abundant with estimated world reserves lasting circa 60 years. Currently, tungsten is typically used as tungsten carbide in cemented carbide used by the metalworking, mining, and construction industries. Nyobolt selected its Tungsten supplier from Germany whose responsible supply chain management procures primary raw materials exclusively from conflict-free sources and makes its products almost entirely from recycled tungsten.
Through Nyobolt’s combined use of ultrafast charging battery science with efficient thermal management that delivers thousands of full charge cycles, the commercial applications which benefit from nearly 24/7 operating uptime are able to downsize battery packs to be lighter, more efficient and fit into smaller cavities, running their machines longer, and as a result, reducing their total cost of ownership as well as their upstream demands on the earth’s critical raw materials.
As the world transitions to a low-carbon, fast-charge future based on technologies that are better for people, industry and the planet, innovation becomes a constant and pivotal process to solve critical problems and expand the horizon of what is possible and sustainable for current and future generations.