High-power pitstop charging …when the need for speed just can’t wait
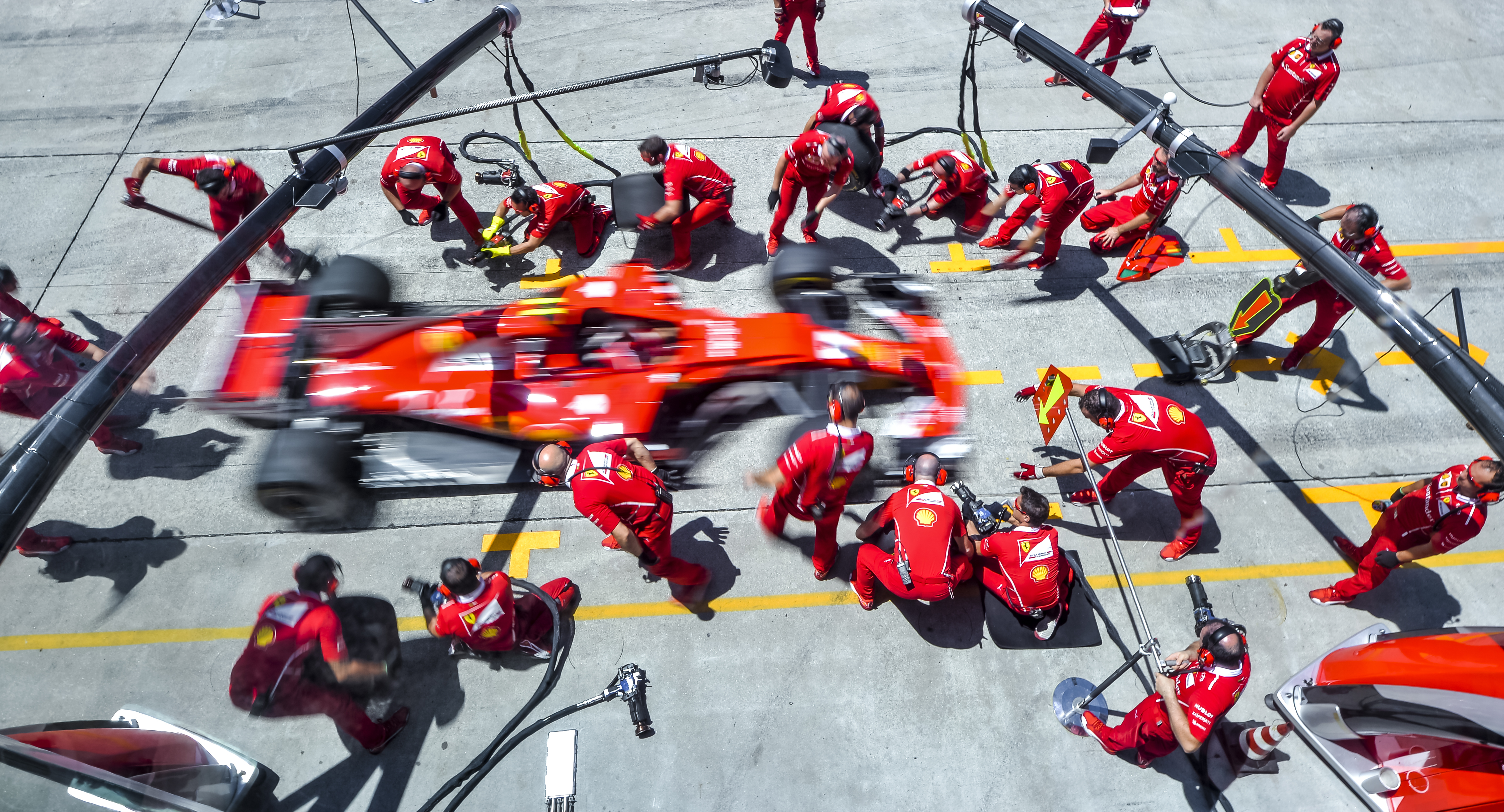
High-power pitstop charging …when the need for speed just can’t wait
A new form of tactical pit stops was introduced to motor racing in 1982 when Gordon Murray targeted a 26-second fuel and tire swap as part of the Brabham team’s race strategy. Today, the time to beat is two seconds for the best-of-the-best in Formula One to pull off a successful pit stop1.
In the Formula E circuit, a delayed introduction of ‘attack charge’ pitstop charging is expected to launch this season which will send a 4 kWh/30 second quick charge to the battery, supporting existing ‘attack mode’ 50 kW power boosts at key moments of the race, sending cars on an accelerated 350 kW joy ride around the track1.
Recently, the pitstop method has proven to be an effective strategy for other applications too. The common denominator being the need for a battery-powered industrial setting, that demand high power and high uptime operations.
Let’s dive into some of them….
Material Handling Warehouse Robotics
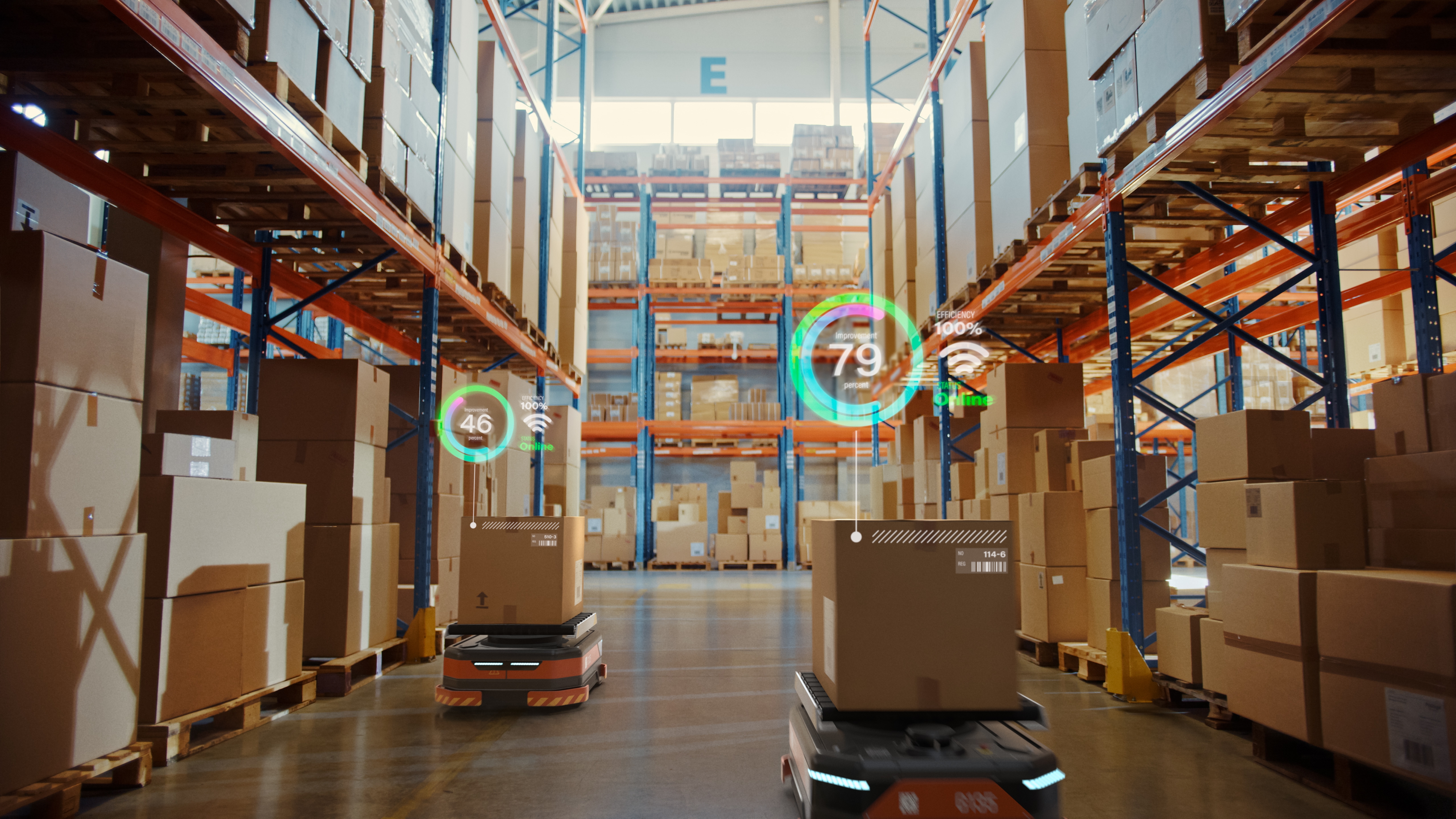
Industry Snapshot
Warehouse robotics and automation adoption are growing at an unprecedented rate to meet the demands of eCommerce and third-party logistics (3PL) efficiency targets, while balancing labor force constraints and increasing inflation. Warehouse robotic operations today are primarily focused on robotic picking, packing, truck loading and unloading and putting away storage. In the Intralogistics Robotics 2023 survey conducted by Modern Materials Handling, 37% of respondents reported using robots in their plants and/or warehouses today, but that number is set to increase to nearly 43% by 20262.
The central economic benefits of adopting a larger robotic fleet in materials warehouse operations are touted as safety and return on investment, while the additional value gained from pairing robotics with AI-powered software systems that improve inventory management, order accuracy and customer satisfaction make an ideal combination for 3PL experts.
Pit Stop Charging Enabler
The introduction of Autonomous Mobile Robots (AMRs) into the material handling industry has substantially increased the productivity of 24/7 warehouse operations. AMRs use advanced sensors, cameras and LiDAR technology to map their surroundings and follow pick-and-place commands without the need for preset routes. However, while AMR manufacturers endorse the productivity benefits of their latest models, each bot is only as valuable as the uptime it delivers, calculated by the power output, range and charge speed of its battery system.
A typical AMR battery today will hold between 300Wh and 1kWh of energy, which is good for around 4-12 hours of operation depending on the duty-cycle. The downtime to replenish the battery can take anywhere between one and eight hours. With the advent of power dense battery cells capable of receiving an ultra-fast charge, each AMR has the potential to fully refuel and be back in circulation in less than five minutes, opening up the charge point for the next AMR to pull in. For warehouse management, that equates to a smaller fleet, operating in faster circulation with less downtime and more billable uptime.
Mine Haul Heavy Duty Operations
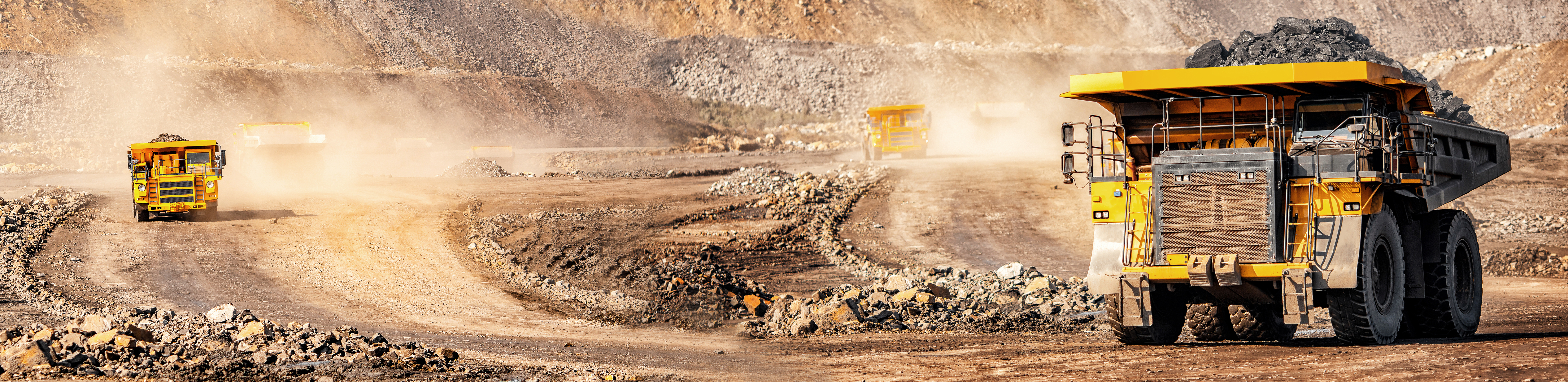
Industry Snapshot
The race gun has been fired for mining companies to electrify the first mining truck fleets with hydrogen or lithium-ion battery powered systems to meet Scope III emission reduction requirements. These beasts provide up to 2MW of power from a 200-300 kWh battery, enough power to tow a 240-tonne truck up and down the mine. Strategic partnerships to supply the first hybrid and electric trial fleets to mines will leverage strengths from OEMs, battery technology companies and mining operators. Examples include projects announced between Toyota and Komatsu, ABB and First Mode, and battery solutions WAE Technologies, mining company Fortescue Metals Group and trucking OEM Liebherr. Industry experts project as many as 1 million diesel mining vehicles will be retrofitted to electric by 20303.
Pit Stop Charging Enabler
Deploying high-power charging infrastructure capable of rapidly re-charging heavy-duty mining trucks pulling a few hundred tonnes of payload will require new megawatt charging systems, and on-board battery technology capable of receiving this extremely high power. Once fleets have adopted high-power electric trucks capable of charging at rates up to 3MW4, strategically positioning high-power DC charging points around the mine will help keep the flow of mining trucks in constant motion. As the new wave of electric mine fleets become increasingly more autonomous, there won’t be a need for human intervention or rest breaks, further driving down charging times and uptime as critical metrics for fleet operators.
Professional Tools and Equipment

Industry Snapshot
The global cordless power tools market makes up ~57% of the total power tools market which is expected to have a 2030 market size of approximately $30 billion5. Even as the range of cordless options in electric drills, axel grinders, saws, and hammers expand and their power output improves, professional construction and maintenance workers know the pain of lugging around a high number of backup battery packs to the job site all too well. Due to the time lost in recharging each appliance on the job, it is more economical to purchase a surplus of portable batteries, recharge them off the clock, and carry the expanded tool kit to every job site.
Pit Stop Charging Enabler
In a recent customer trial, Nyobolt supplied a leading professional tools & appliances customer with an 18V ultra-fast charging battery and charger kit that brought its drill back to life in less than 5 minutes. In an ultra-efficient work mode, one battery pack could even be used to do multiple jobs in a row swapping from one tool to another, recharging during short rest breaks or lunch. Overall, this would result in a reduction in backup battery costs with no loss in efficiency and uptime.
Last Mile Delivery Drones
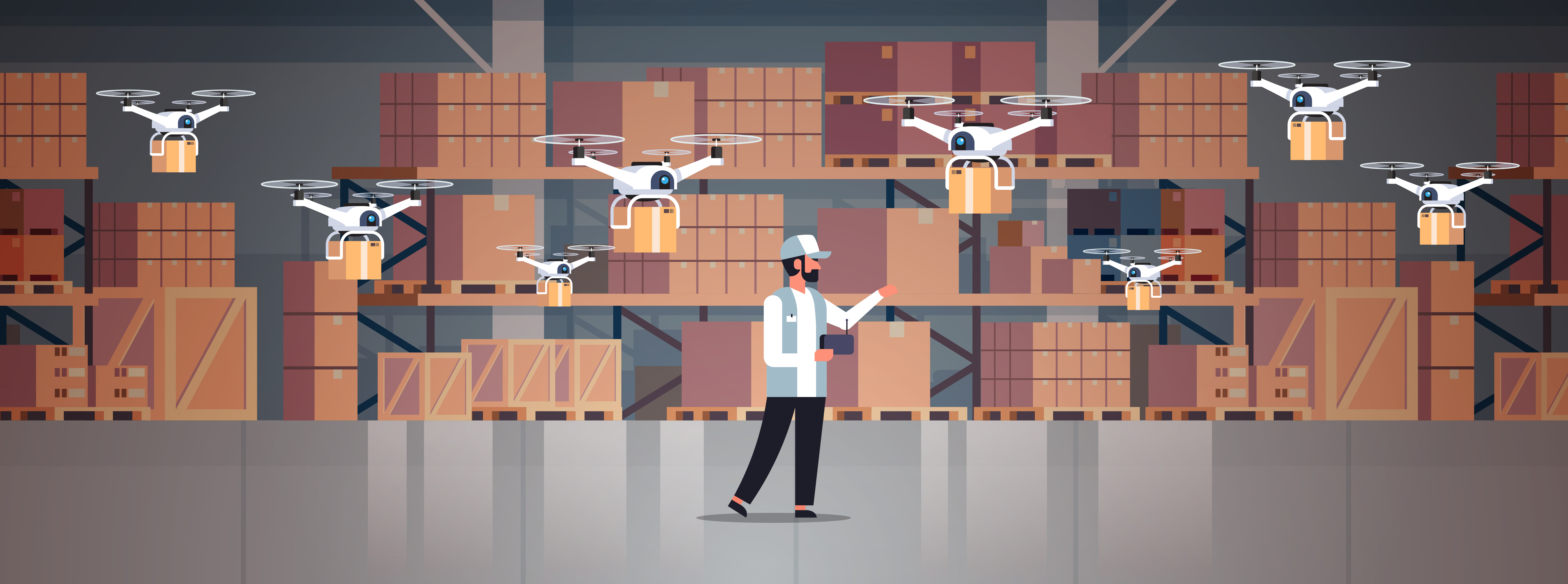
Industry Snapshot
Drone technologies are emerging in various form factors to solve a variety of industry demands, from eCommerce goods delivery to emergency disaster relief, logistics, and transportation services. Drones also have important environmental and economic benefits as it is expected that drones will be responsible for 20% of deliveries by 2028, reducing pressure on ground transportation, while estimated to cost around $1.23 per delivery compared to $5.33 for a four-mile distance by electric van6.
As an example of the convenience, efficiency and time savings of drone delivery in practice, take Zipline – an early pioneer in drone delivery services, who launched their first successful pilot delivering emergency blood supply to rural hospitals in Rwanda in 2016. Today, Zipline has launched two autonomous electric drones “Zips” which serve healthcare, restaurants, convenience and grocery, and agriculture industries with a fully integrated warehousing, fulfillment, and charging model. The P1 Zip has a round trip range capacity of 120 miles up to 60 mph on a single charge and can carry packages up to 4 lbs. The larger P2 Zip can double its payload and increase its speed to 70 mph but is limited to a 24-mile round trip circuit. Zipline customers like Walmart promise customers convenient, fast delivery within as little as ten minutes backed by efficient platform monitoring to keep drones “up” time high and reduce fleet costs for the retailer7.
Pit Stop Charging Enabler
High utilisation of relatively light, high-powered delivery drones require centralised depot charging solutions that can replenish a small battery in just a few minutes, or approximately the time it takes for new packages to be loaded onto the drone and sent off on its next flight. Operators such as Zipline, Walmart and Amazon are targeting millions of miles in extremely fast and convenient customer deliveries. To fulfill this promise, each drone’s battery system needs to be designed to maintain its capacity well above its 120-mile range over thousands of rapid charge cycles.
Not to toot our own horn here (well, ok maybe we are), but Nyobolt’s Xtreme ultra-high power battery cells have completed well over 10,000 5-minute fast charges with minimal degradation in our internal testing. That downtime is the perfect pitstop for fulfilling a new drone delivery order while grabbing a quick top-up on the charger. Nyobolt’s modular pouch cells come in 3Ah and 23Ah sizes and are perfectly fit-for-purpose for drone delivery operations that have a need for speed and high overall fleet efficiency.
Sources:
- automobilist.com
- mmh.com
- mining-technology.com
- im-mining.com
- Masan High-Tech Materials study, 2020
- sciencedirect.com
- flyzipline.com