Giant Electrification – The Challenge in Electrifying Surface Mine Haul Trucks
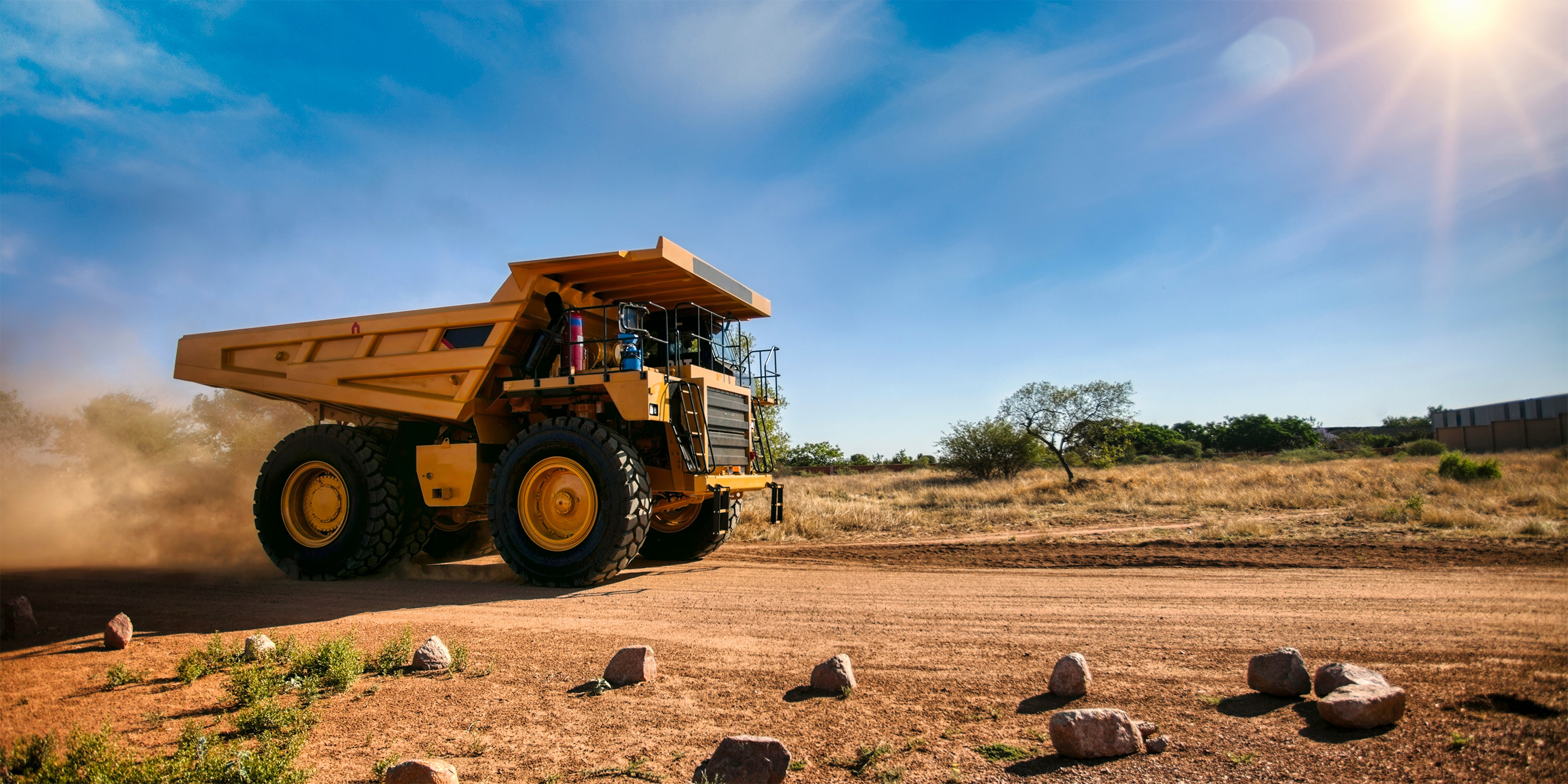
When considering CO2 abatement and operating cost savings provided through the decarbonisation of the transportation industry, it’s essential to include heavy-duty offroad vehicles such as mine haul trucks which are one of the single most polluting asset classes primed and ready for electrification.
For the last few years, there have been several promising collaborations between mining companies and OEMs intent on reducing Scope 1 emissions through switching to alternative clean energy sources to power the fleet while reducing the total cost of ownership at the same time. Despite technological innovations in hydrogen and battery-electric systems, there has been slow adoption of the proposed alternatives to diesel-powered mining trucks. For example, Rio Tinto has indicated that fully electrifying their haul trucks will likely not happen at scale until after 2030, due to the need for significant innovation in battery density, charging speed, and overall reliability.
Battery-Electric Vehicles (BEVs):
In surface mining, which makes up 80% of the majority of the global mine truck fleet, achieving net-zero targets while maintaining near 24/7 run-time and a low total cost of ownership is a formidable challenge with traditional lithium-ion batteries. The problem is that the number of traditional energy cells (such as LFP or NMC) required to achieve the power capable of propelling a 500 tonne truck around the mine drives the pack size up to as much as 1MWh, becoming extremely heavy and compromising the structural integrity of the truck, accelerating tyre wear, and decreasing the payload (thereby decreasing production volume). Traditional lithium-ion battery technology also has a very low charge rate (1-2C on average) causing a full BEV truck to be out of service for several hours to recharge, assuming MW-level DC charging infrastructure is available. Furthermore, charging from a MW-level DC charger would more rapidly degrade the traditional lithium-ion battery cells, requiring more frequent replacements. With an initial upfront cost nearing $5 million per truck, plus the higher estimated running costs and lower operating uptime, the investment in a full BEV fleet with existing lithium-ion battery technology would be unfounded.
Therefore, we identify two key opportunities for a new class of power batteries which can solve existing pain points in mine-haul electrification:
- Battery systems can be appropriately sized with the right mix of power and energy to charge at higher rates of at least 4C, while at the same time being able to accept an incredibly powerful level of regenerative energy (regen) when going down the mine or while slowing down. The stored regen energy and higher power acceptance will reduce charging requirements and approach 24/7 operating requirements.
- Battery cells that are able to withstand longer charge-discharge cycles at high-power rates without significant degradation will provide a more attractive return on investment (ROI) for fleet operators. The ideal battery replacement schedule would follow the current service and maintenance schedule for heavy-duty components such as engines or longer.
Hybrid Electric Vehicles (HEVs):
While widespread full BEV mine-haul electrification is likely 5-10 years away, HEV mine trucks are becoming a pragmatic bridge solution to prove out new advancements in power batteries with lower capex while immediately reducing emissions and fuel costs on Day 1.
Hybrid vehicles use energy generated from the braking of the vehicle, or when it’s going downhill, to recharge the battery. The difference with traditional lithium-ion batteries with high energy density, but low power density is that they cannot accept the considerable amount of energy coming off of the wheels when braking, and so dispel much of that energy as heat waste. But with a high-power battery HEV which can recapture that same kinetic energy otherwise wasted as heat, multiple benefits are applied to the fleet:
- Regen energy is captured and stored as energy in the battery pack, extending its range
- No charging infrastructure investment immediately required leading to lower capex
- Fuel savings of up to 30% per truck per year are saved immediately
- Emissions savings of up to 20,000 tonnes of CO2e per truck per year
- Fleet operators recognize immediate savings, recovering their ROI quickly
It’s a gargantuan problem that will not be solved one fleet at a time, but one truck at a time. Mine site operators need time to build confidence that the transition from diesel to HEV to BEV mine haul trucks will not only deliver the same operational run time but reduce the fleet’s total cost of ownership and reduce Scope 1 emissions all in one. We’d like to call it the ‘Mining Trifecta’.